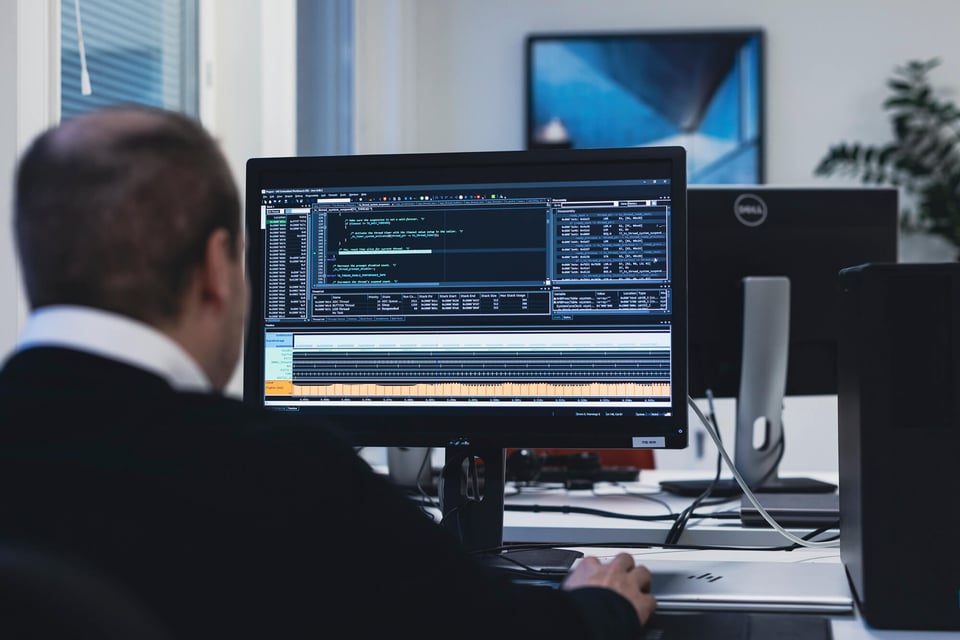
All-in-one toolchain
IAR Embedded Workbench offers a fully integrated development environment (IDE) with an advanced optimizing compiler, linker, assembler, and debugger, eliminating the need for multiple third-party tools.
Product
IAR Embedded Workbench is a complete development toolchain with an optimized compiler, debugger, and analysis tools, streamlining embedded software development across various microcontrollers and processor architectures for performance and reliability.
IAR Embedded Workbench combines advanced debugging, broad device support, and industry compliance, enabling efficient, reliable, and secure embedded development across diverse architectures
IAR Embedded Workbench offers a fully integrated development environment (IDE) with an advanced optimizing compiler, linker, assembler, and debugger, eliminating the need for multiple third-party tools.
The highly optimized IAR C/C++ Compiler delivers industry-leading performance, allowing developers to create highly efficient embedded applications with minimal code size and power consumption.
The built-in IAR C-SPY Debugger provides advanced debugging capabilities, including real-time trace, code coverage, function profiling, and RTOS awareness for precise debugging and system optimization.
From advanced debugging to seamless IDE integration and RTOS support, IAR Embedded Workbench helps developers optimize performance, ensure compliance, and accelerate time to market.
Use IAR C-STAT for static code analysis to enforce coding standards and IAR C-RUN* for runtime error detection, helping identify vulnerabilities, improve reliability, and ensure high-quality embedded applications.
*Available for Arm and RX.
IAR Embedded Workbench is certified by TÜV SÜD to meet multiple functional safety standards. Each new platform release undergoes certification, ensuring consistently high-quality development processes and software.
Arm | RISC-V | Renesas RL78 | Renesas RH850 | Renesas RX | STM8 | AVR32 | MSP430 | 8051 | AVR | Renesas 78K | Renesas V850 | Renesas M16/C/R8C | |
IAR Embedded Workbench | |||||||||||||
FuSa certified | |
Develop your IAR Embedded Workbench projects directly in Visual Studio Code with our powerful extensions. Discover how IAR is revolutionizing embedded development with C-SPY Listwindows, featuring tools like Registers, Symbolic Memory, Live Watch, Trace, Profiling, and Code Coverage.
Enhance your Eclipse IDE for C/C++ Developers with the free IAR Eclipse plugins, enabling seamless integration with IAR Embedded Workbench. Leverage high-quality IAR build toolchains and advanced debugging features for supported target architectures.
Combine Zephyr’s flexibility with IAR’s reliability: optimized builds, RTOS-aware debugging, and safety-certified toolchains for modern embedded systems.
Language | Supported standards | Standard libraries |
C | ISO/IEC 9899:2018 ISO/IEC 9899:1990 ISO/IEC 9899:1995 |
C standard library
|
C++ | ISO/IEC 14882:2017 | ISO/IEC 14882:2014 ISO/IEC 14882:2017
|
*Legacy compilers might not support the latest standards.
How to get started
Migration help
Smoothly transition your existing project to IAR Embedded Workbench with our migration tools and comprehensive documentation.
EWPtool simplifies the migration process, whether you’re moving to IAR Embedded Workbench or upgrading between toolchain versions.
Download EWPtool now on GitHub for a smooth and efficient migration!
Migration guides are available for 8051, MSP430, Arm, Renesas RX, and Renesas RL78.
For more resources, visit IAR MyPages.
Contact our experienced FAEs, who will help take you further.
IAR Embedded Workbench supports a wide range of microcontrollers, including Arm, RISC-V, 8051, MSP430, AVR, AVR32, Renesas RX, Renesas RL78, Renesas RH850, Renesas V850, M16C/R8C, Renesas 78K, and STM8. Legacy architectures such as ColdFire, CR16C, H8, HCS12, M32C, MAXQ, R32C, S08, SAM8, and SH are available by request only.
By integrating compilation, debugging, and analysis in a single environment, developers can reduce context switching and streamline their workflow.
Yes, IAR Embedded Workbench includes certified tools for functional safety development, with TÜV SÜD-certified versions available for compliance with industry safety standards.
Yes, IAR Embedded Workbench integrates with VS Code via the IAR Build and Debug extensions, allowing developers to code and debug using a modern interface. It also supports Eclipse IDE through plug-ins for workflow compatibility. Additionally, it can be integrated with third-party build and CI/CD systems such as Jenkins, GitHub Actions, and GitLab CI/CD using IAR Build Tools. This ensures flexibility for teams that work in hybrid development environments.
Yes, the toolchain supports third-party RTOS debugging extensions such as FreeRTOS, Azure RTOS, Zephyr RTOS and PX5 RTOS. It also allows the use of middleware libraries, including TCP/IP stacks, file systems, and security frameworks. Additionally, it is compatible with hardware debugging tools from vendors like Segger, PE Micro, and Renesas, TI, and more, enabling cross-platform debugging.
Programming, Functional safety, Debugging, CI/CD
Programming, Code quality, Debugging, Embedded DevOps
Resources